
86 17344894490
service@chalcoaluminum.com
- Ânodo sacrificial de liga de alumínio
- Ânodo sacrificial de liga de magnésio
- Série de proteção catódica atual impressionada
Peças estruturais de perfil de alumínio extrudados na fabricação de veículos
De acordo com as informações, cerca de 60% das encomendas existentes de fabricantes europeus de locomotivas e veículos são veículos com carroceria de alumínio. Há 20 anos, tais pedidos eram de apenas 2% a 3%. Agora, a estrutura de alumínio foi aplicada no gelo, tgv-2n, etr460, etr500, trem do Talgo Hotel e outros trens de alta velocidade, bem como muitos veículos de transporte ferroviário suburbano e urbano.
A adoção de peças estruturais de perfil de alumínio extrudado começou no início da década de 1970. Naquela época, o progresso científico e tecnológico na aplicação de perfis de alumínio possibilitou a fabricação de componentes de alumínio de acordo com a forma e o tamanho necessários. Este componente de alumínio foi aplicado à carroceria inclinada dos trens aptos na Grã-Bretanha. No entanto, naquela época, a aplicação de componentes de alumínio extrudado não produziu grandes benefícios, ou seja, os preços mais altos do material não foram compensados pela redução da carga de trabalho de fabricação. Naquela época, o uso de peças estruturais de grande porte só reduziu a carga de trabalho de produção da carroceria do carro em 40%, e reduziu o peso morto da carroceria de 26m de comprimento para 7,5t, enquanto o peso morto da carroceria de aço de 26m de comprimento era de 11T. Na década de 1970, o departamento ferroviário prestou mais atenção ao cálculo do custo total de toda a vida útil dos veículos (custo de compra mais custo de operação e manutenção). Eles perceberam que o consumo de energia de tração de trem deve ser mantido no mesmo nível, o que depende em grande parte do auto peso do material circulante.
Posteriormente, algumas novas medidas técnicas e tecnológicas, a mais importante das quais foi alcançada em meados da década de 1980, como a adoção do método de extrusão de peças estruturais de grande porte de concha de camada dupla, que reduziu a necessidade de fixações transversais ao mínimo, reduziu ainda mais o tempo de produção do corpo de alumínio veicular, reduzido em 50% em relação aos veículos de aço, e tem sido possível fazer corpo de cilindro de dupla camada de acordo com o método convencional, e então a abertura de furos de janela As operações de soldagem são todas concluídas no processo de operações técnicas unificadas, usando apenas parcialmente tecnologia e equipamento robô.
Agora, quando os departamentos ferroviários reduzem gradual e mais sua participação no desenvolvimento de novos veículos e implementem políticas de compra para reduzir os custos iniciais de fabricação e despesas operacionais futuras, os fabricantes têm maior liberdade em adotar novas estruturas e materiais para atender às exigências técnicas dos assinantes e se adaptar à tendência de desenvolvimento do mercado. As peças estruturais de perfil de alumínio extrudadas também têm outras vantagens em atender a alguns requisitos rigorosos para a estrutura do veículo. Por exemplo, a rigidez da estrutura de extrusão de conchas de camada dupla pode garantir que o impacto aerodinâmico produzido quando o trem de alta velocidade se encontra tenha uma força de impacto especial. Outra característica importante da carroceria com esta estrutura é sua grande rigidez longitudinal. A razão de rigidez longitudinal e transversal pode chegar a 70:30, enquanto a razão da carroceria do carro de aço é de 40:60. Além disso, os perfis de alumínio também podem atender aos requisitos de boa forma externa, sem o uso de enchimentos e muito trabalho manual. Por exemplo, para alguns modelos da Ferrovia Federal Alemã, já que não é utilizado nenhum enchimento, após o cálculo, juntamente com o revestimento de tinta, o auto peso pode ser de 500kg.
O uso de peças estruturais de perfil de alumínio extrudado também faz com que os fabricantes de veículos enfrentem tarefas complexas. Eles devem encontrar um equilíbrio entre os preços do trabalho e do material, e fazer com que os designers se esforcem para alcançar esse equilíbrio. Deve-se esclarecer que o material é apenas um fator em todo o conceito. O processo produtivo e o processo técnico adotado também devem ser formulados em detalhes para que esteja em conformidade com a capacidade de produção do empreendimento e equilibre com o investimento.
Por exemplo, para a maioria das empresas fabricantes de máquinas, minimizar as reservas de meios de produção é uma prioridade máxima. A escolha de materiais e processos pelos designers tem um impacto significativo nisso. A ABB possui uma linha de produção que pode produzir 8 veículos com corpo de alumínio a cada semana, o que reduz o custo total de armazenamento do material em 8%. No entanto, esse equilíbrio é facilmente destruído devido às mudanças no processo técnico causadas pelo uso de materiais. Por exemplo, quando a transição da soldagem para a ligação requer mais reservas diárias para compensar o tempo considerável necessário para o endurecimento do vínculo.
Outro fornecedor líder de perfis de alumínio para a fabricação de material circulante é a empresa alemã VAW. Os líderes da empresa preveem que há uma grande tendência de desenvolvimento na padronização da estrutura veicular e na adoção do método de design de módulos (essa tendência tem sido reforçada devido à demanda do mercado, por isso conta com o apoio dos fabricantes), e acreditam que considerando a demanda de mercado para a regionalização do transporte ferroviário local na Alemanha, algumas empresas privadas prestarão mais atenção ao uso da estrutura padronizada do módulo para atender aos requisitos individuais dos ordenadores em maior medida. Atualmente, vários fabricantes europeus de locomotivas e veículos têm um grande número de ideias de design, e essas ideias são baseadas no design do módulo. Essa transformação para padronização e modularidade é benéfica tanto para os produtores quanto para os usuários. A expansão do uso de perfis de alumínio na fabricação de veículos reduzirá consideravelmente o ciclo de produção devido ao uso mais amplo da soldagem automática.
Também é óbvio que os veículos de corpo de alumínio soldado têm alta resistência à carga de impacto, o que é propício para melhorar a segurança na condução. A ABB investiu 1 milhão de libras para organizar e realizar o teste de destruição da estrutura de alumínio, e obteve resultados satisfatórios e mais importantes, os resultados esperados dos testes. A empresa também acumulou valiosa experiência prática na reparação dos métodos de falha dos veículos acidentais. No início de 1994, o teste de dano na amostra de teste de carro de passageiros do tgv-2n encomendado pelo GEC Alstom na França provou que quando a força de impacto era de 250t, devido à energia de impacto absorvida de 8mj, a estrutura foi extrudada por um total de 80cm, e o corpo de alumínio permaneceu intacto como um todo.
Ao mesmo tempo, o reconhecimento das vantagens da carroceria do carro de alumínio não é sem problemas. A locomotiva do corpo de aço e os fabricantes de veículos expressaram preocupação com a ênfase no alumínio no processo de fabricação de trens de gelo na Alemanha, e realizaram um estudo para confirmar a superioridade do aço em 1994. No entanto, como antes, o uso da estrutura de aço leva a um aumento de cerca de 20% no peso morto da carroceria do carro.
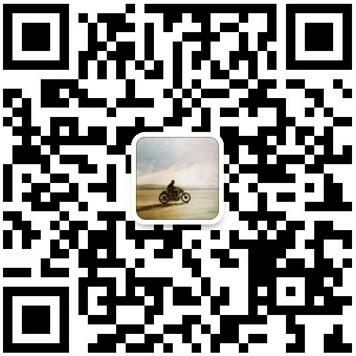
Oferta gratuita de produtos, bem-vindo para consultar a qualquer momento, daremos a primeira resposta. Nosso e-mail: